List of WORK PROCESS
"Customer requirements are kept in mind at all stages of the order process."

TAKE ORDER
During the order process obtain as much information possible from customers regarding their specific product needs. Detailed specification drawings are used to come up with the best possible solution for the required process. The drawings and precise measurements are than passed onto the manufacturing for processing.
BUY RAW MATERIAL
Depending on the customer requirement, the best possible raw materials and scrap is sourced from one of our trusted suppliers. Once the scrap arrives it is checked to make certain there are no quality issues and it is to the top most quality available.


COMBING THE APPROPRIATE
RAW MATERIALS
The appropriate raw materials are then precisely weighed ready to be combined and melted. Different components have different uses therefore; the durability of each component is different so the combinations of metals are also altered depending on the final component.
MELTING THE SCRAP
IN THE FOUNDRY
Melting of the scrap is performed in a furnace. The process of melting the scrap is a vital stage in the process, during this stage the metal chemistry needs to be adjusted according to the intended final use of the product. Our manufacturing team are well trained in this area of the process to make these alterations.


BILLET CASTING / CUTTING / HEATING
Once metal melting and cast in to billet shape, then we cutting that billet in to customer requirement size. and then we inspect each and every billet for final product. before that we heating that billet at certain temperature for pressing into extrusion press machine.
BAR EXTRUSION
This is the final stage of production. Extrusion Presses push hot billets through dies to produce a variety of long, uniformly rod, profile, sections and more as per costumer design and requirement. For that we have 750ton extrusion press.
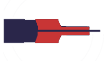

TURNING / MACHINING
This is the final stage of the process it usually involves grinding, sanding, or machining the component in order to achieve the desired dimensional accuracies, physical shape and surface finish required by the customer.
QUALITY CHECK
During the production, brass is subject to constant evaluation and control of the materials and processes used to form specific brass stock. The chemical compositions of the raw materials are checked and adjusted before melting. The heating and cooling times and temperatures are specified and monitored. The thickness is measured at each step. Finally the, the finished products are tested for hardness, strength, dimensions, and other factors to ensure they meet the required specifications.


PACKING/DISPATCH
The final products are packed in such a way that no products can be damaged in transit. All products like rod, profile, sections and Components are packing with proper wooden box for export and plastic wrap for local. All orders are completed and dispatched to the customer to be delivered in the time frame required.